Szafy sterownicze odgrywają kluczową rolę w automatyzacji procesów przemysłowych, zapewniając centralne miejsce do zarządzania i kontrolowania różnych urządzeń elektrycznych oraz elektronicznych. Ich główną funkcją jest ochrona komponentów przed uszkodzeniami mechanicznymi, wilgocią oraz zanieczyszczeniami, co jest szczególnie istotne w trudnych warunkach przemysłowych. Szafy te są zazwyczaj wykonane z materiałów odpornych na korozję i mają odpowiednią klasę szczelności, co pozwala na ich długotrwałe użytkowanie. Wewnątrz szaf znajdują się różnego rodzaju elementy, takie jak przekaźniki, styczniki, a także systemy sterowania PLC, które umożliwiają automatyzację procesów. Dzięki zastosowaniu szaf sterowniczych możliwe jest zdalne monitorowanie i kontrolowanie pracy maszyn, co zwiększa efektywność produkcji oraz minimalizuje ryzyko awarii. Dodatkowo, szafy te mogą być wyposażone w różnorodne systemy zabezpieczeń, takie jak wyłączniki nadprądowe czy bezpieczniki, które chronią instalację przed przeciążeniem oraz zwarciem.
Jakie materiały są używane do produkcji szaf sterowniczych
Produkcja szaf sterowniczych opiera się na wykorzystaniu różnych materiałów, które zapewniają nie tylko trwałość, ale także odpowiednie właściwości ochronne. Najczęściej stosowanym materiałem jest stal nierdzewna, która charakteryzuje się wysoką odpornością na korozję oraz uszkodzenia mechaniczne. Stal nierdzewna jest idealnym wyborem w środowiskach o dużej wilgotności lub narażonych na działanie substancji chemicznych. Innym popularnym materiałem jest stal ocynkowana, która również oferuje dobrą odporność na korozję, ale jest mniej kosztowna niż stal nierdzewna. W przypadku zastosowań w mniej wymagających warunkach można również spotkać szafy wykonane z tworzyw sztucznych, które są lekkie i łatwe w obróbce. Warto zwrócić uwagę na to, że wybór odpowiednich materiałów ma kluczowe znaczenie dla funkcjonalności i trwałości szaf sterowniczych. Dodatkowo, producenci często oferują różne powłoki ochronne, które zwiększają odporność na czynniki zewnętrzne oraz poprawiają estetykę urządzeń.
Jakie są najważniejsze aspekty projektowania szaf sterowniczych
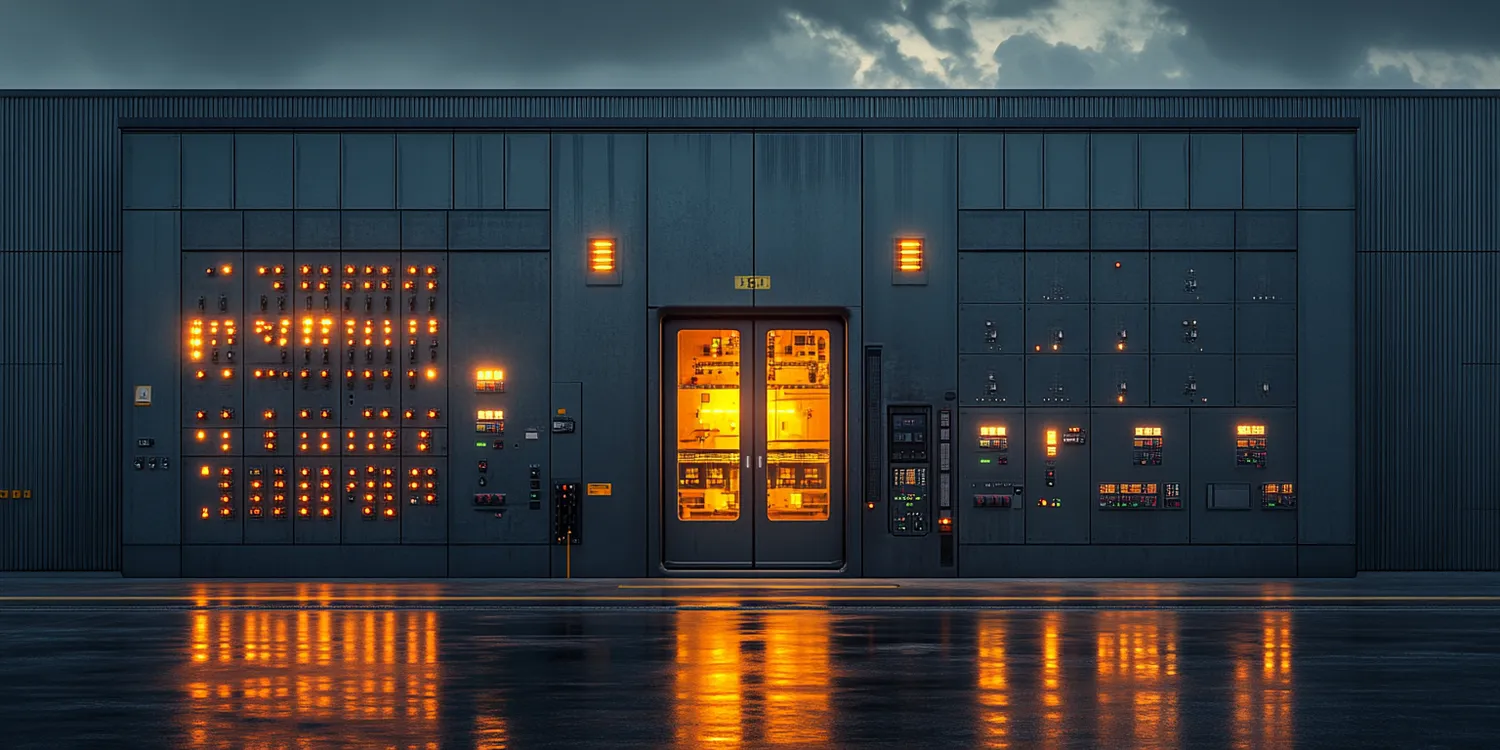
Projektowanie szaf sterowniczych to skomplikowany proces, który wymaga uwzględnienia wielu czynników technicznych oraz ergonomicznych. Kluczowym aspektem jest określenie wymagań dotyczących przestrzeni wewnętrznej szafy, aby pomieścić wszystkie niezbędne komponenty oraz umożliwić ich łatwy dostęp podczas konserwacji czy napraw. Ważne jest również zaprojektowanie odpowiedniego układu wentylacji, aby zapewnić optymalne warunki pracy dla urządzeń elektronicznych i uniknąć przegrzewania się podzespołów. Kolejnym istotnym elementem jest dobór odpowiednich systemów zabezpieczeń oraz oznaczeń, które ułatwią identyfikację poszczególnych komponentów i zwiększą bezpieczeństwo użytkowników. Projektanci muszą także brać pod uwagę normy i przepisy dotyczące bezpieczeństwa elektrycznego oraz ochrony środowiska, co wpływa na wybór materiałów oraz technologii produkcji. Również estetyka szafy ma znaczenie; dobrze zaprojektowana obudowa powinna być nie tylko funkcjonalna, ale także estetyczna i pasować do otoczenia przemysłowego.
Jakie są różnice między szafami sterowniczymi a rozdzielnicami elektrycznymi
Szafy sterownicze i rozdzielnice elektryczne to dwa różne typy urządzeń stosowanych w instalacjach elektrycznych, które pełnią odmienne funkcje. Szafy sterownicze koncentrują się głównie na automatyzacji procesów przemysłowych oraz kontroli urządzeń elektrycznych poprzez zastosowanie systemów sterowania i monitorowania. Zawierają one elementy takie jak programowalne sterowniki logiczne (PLC), czujniki oraz przekaźniki, które umożliwiają zdalne zarządzanie pracą maszyn. Z kolei rozdzielnice elektryczne służą przede wszystkim do rozdzielania energii elektrycznej pomiędzy różnymi obwodami oraz zabezpieczania ich przed przeciążeniem lub zwarciem. W rozdzielnicach znajdują się wyłączniki nadprądowe, bezpieczniki oraz inne elementy zabezpieczające. Różnice te wpływają również na konstrukcję obu urządzeń; podczas gdy szafy sterownicze często mają bardziej skomplikowaną budowę ze względu na dodatkowe komponenty elektroniczne, rozdzielnice są zazwyczaj prostsze w budowie i skoncentrowane na funkcji dystrybucji energii.
Jakie są kluczowe zalety stosowania szaf sterowniczych w automatyce
Stosowanie szaf sterowniczych w automatyce przemysłowej przynosi wiele korzyści, które znacząco wpływają na efektywność i bezpieczeństwo procesów produkcyjnych. Jedną z najważniejszych zalet jest centralizacja zarządzania urządzeniami, co umożliwia łatwe monitorowanie ich pracy oraz szybką reakcję na ewentualne awarie. Dzięki zastosowaniu nowoczesnych systemów sterowania, operatorzy mogą zdalnie kontrolować maszyny, co znacznie zwiększa komfort pracy oraz pozwala na oszczędności związane z zatrudnieniem personelu. Szafy sterownicze są również projektowane z myślą o łatwej konserwacji; dostęp do komponentów wewnętrznych jest zazwyczaj dobrze przemyślany, co ułatwia przeprowadzanie napraw i wymianę części. Kolejnym atutem jest możliwość dostosowania szaf do specyficznych potrzeb danego zakładu produkcyjnego; producenci oferują różnorodne rozwiązania, które można dostosować do indywidualnych wymagań klientów. Dodatkowo, szafy te często wyposażone są w zaawansowane systemy zabezpieczeń, co zwiększa bezpieczeństwo zarówno urządzeń, jak i pracowników.
Jakie są najczęściej spotykane błędy przy instalacji szaf sterowniczych
Instalacja szaf sterowniczych to proces wymagający precyzji oraz znajomości zasad bezpieczeństwa, jednak często popełniane są błędy, które mogą prowadzić do poważnych konsekwencji. Jednym z najczęstszych problemów jest niewłaściwe podłączenie przewodów elektrycznych, co może skutkować zwarciem lub uszkodzeniem sprzętu. Ważne jest, aby przed rozpoczęciem instalacji dokładnie zapoznać się z dokumentacją techniczną oraz schematami połączeń. Innym powszechnym błędem jest niedostateczne zabezpieczenie szafy przed działaniem czynników zewnętrznych, takich jak wilgoć czy kurz; brak odpowiednich uszczelnień może prowadzić do awarii komponentów wewnętrznych. Często zdarza się także, że nie uwzględnia się wymagań dotyczących wentylacji, co może prowadzić do przegrzewania się urządzeń i ich uszkodzenia. Ponadto, niewłaściwe rozmieszczenie elementów wewnętrznych może utrudniać dostęp do nich podczas konserwacji, co wydłuża czas napraw i zwiększa koszty eksploatacji.
Jakie są nowoczesne technologie wykorzystywane w szafach sterowniczych
Nowoczesne technologie mają ogromny wpływ na rozwój szaf sterowniczych, wprowadzając innowacyjne rozwiązania, które zwiększają ich funkcjonalność oraz efektywność. Jednym z najważniejszych trendów jest integracja systemów IoT (Internet of Things), które umożliwiają zdalne monitorowanie i zarządzanie pracą urządzeń za pomocą aplikacji mobilnych lub komputerowych. Dzięki temu operatorzy mogą na bieżąco śledzić parametry pracy maszyn oraz szybko reagować na ewentualne nieprawidłowości. Kolejnym istotnym rozwiązaniem są inteligentne systemy diagnostyczne, które analizują dane z czujników umieszczonych w szafach sterowniczych i informują o konieczności przeprowadzenia konserwacji lub wymiany komponentów. Warto również zwrócić uwagę na rozwój technologii komunikacyjnych; nowoczesne szafy często wyposażone są w protokoły komunikacyjne takie jak Modbus czy Profibus, co umożliwia łatwą integrację z innymi systemami automatyki. Dodatkowo, coraz częściej stosuje się zaawansowane systemy zabezpieczeń, takie jak monitoring wideo czy czujniki ruchu, które zwiększają bezpieczeństwo zarówno urządzeń, jak i osób pracujących w pobliżu.
Jakie są trendy w projektowaniu szaf sterowniczych na przyszłość
W miarę rozwoju technologii oraz rosnących wymagań rynku przemysłowego projektowanie szaf sterowniczych ewoluuje w kierunku bardziej zaawansowanych rozwiązań. Jednym z kluczowych trendów jest miniaturyzacja komponentów elektronicznych, co pozwala na tworzenie mniejszych i bardziej kompaktowych szaf bez utraty funkcjonalności. Dzięki temu możliwe jest oszczędzanie przestrzeni w zakładach produkcyjnych oraz uproszczenie instalacji. Kolejnym istotnym kierunkiem rozwoju jest zwiększona automatyzacja procesów projektowania i produkcji szaf sterowniczych; wykorzystanie narzędzi CAD oraz symulacji komputerowych pozwala na szybsze i bardziej precyzyjne opracowywanie nowych modeli. Warto również zauważyć rosnącą popularność ekologicznych rozwiązań; producenci coraz częściej stawiają na materiały przyjazne dla środowiska oraz energooszczędne technologie. Dodatkowo, integracja sztucznej inteligencji w systemach zarządzania pozwala na jeszcze lepsze monitorowanie pracy maszyn oraz optymalizację procesów produkcyjnych.
Jakie normy i przepisy regulują produkcję szaf sterowniczych
Produkcja szaf sterowniczych podlega wielu normom i przepisom mającym na celu zapewnienie bezpieczeństwa użytkowników oraz niezawodności działania urządzeń. W Europie kluczowym dokumentem regulującym te kwestie jest dyrektywa maszynowa 2006/42/WE, która określa wymagania dotyczące bezpieczeństwa maszyn oraz ich komponentów. Producenci muszą również przestrzegać norm EN 61439 dotyczących rozdzielnic niskonapięciowych oraz EN 60529 dotyczących stopni ochrony obudów przed ciałami stałymi i wodą (klasy IP). Normy te definiują m.in. wymagania dotyczące materiałów używanych do produkcji obudów oraz testy odporności na różne czynniki zewnętrzne. W przypadku zastosowań przemysłowych istotne są także przepisy dotyczące ochrony przeciwpożarowej oraz ochrony środowiska; producenci muszą zapewnić odpowiednie certyfikaty potwierdzające zgodność swoich produktów z obowiązującymi normami ekologicznymi. Dodatkowo, wiele firm decyduje się na wdrażanie systemów zarządzania jakością ISO 9001, co pozwala na ciągłe doskonalenie procesów produkcyjnych oraz zwiększenie satysfakcji klientów.
Jakie są koszty związane z zakupem i eksploatacją szaf sterowniczych
Koszty związane z zakupem i eksploatacją szaf sterowniczych mogą być bardzo zróżnicowane i zależą od wielu czynników takich jak rodzaj zastosowanych materiałów, skomplikowanie projektu czy dodatkowe wyposażenie. Przy zakupie należy uwzględnić nie tylko cenę samej obudowy, ale także koszt komponentów wewnętrznych takich jak styczniki, przekaźniki czy systemy sterowania PLC. Koszt ten może znacząco wzrosnąć w przypadku zastosowania zaawansowanych technologii czy specjalistycznych rozwiązań dostosowanych do indywidualnych potrzeb klienta. Ponadto warto pamiętać o kosztach związanych z instalacją; niewłaściwe podłączenie lub brak doświadczenia ekipy montażowej mogą prowadzić do dodatkowych wydatków związanych z naprawami czy przestojami produkcyjnymi.